Smart Industry Capacity Booster
This project is part of the NXTGEN Smart Industry programme, which aims to be a leader in Europe with the best and most flexible manufacturing ecosystem/network.
Centre of Expertise Digital Operations & Finance
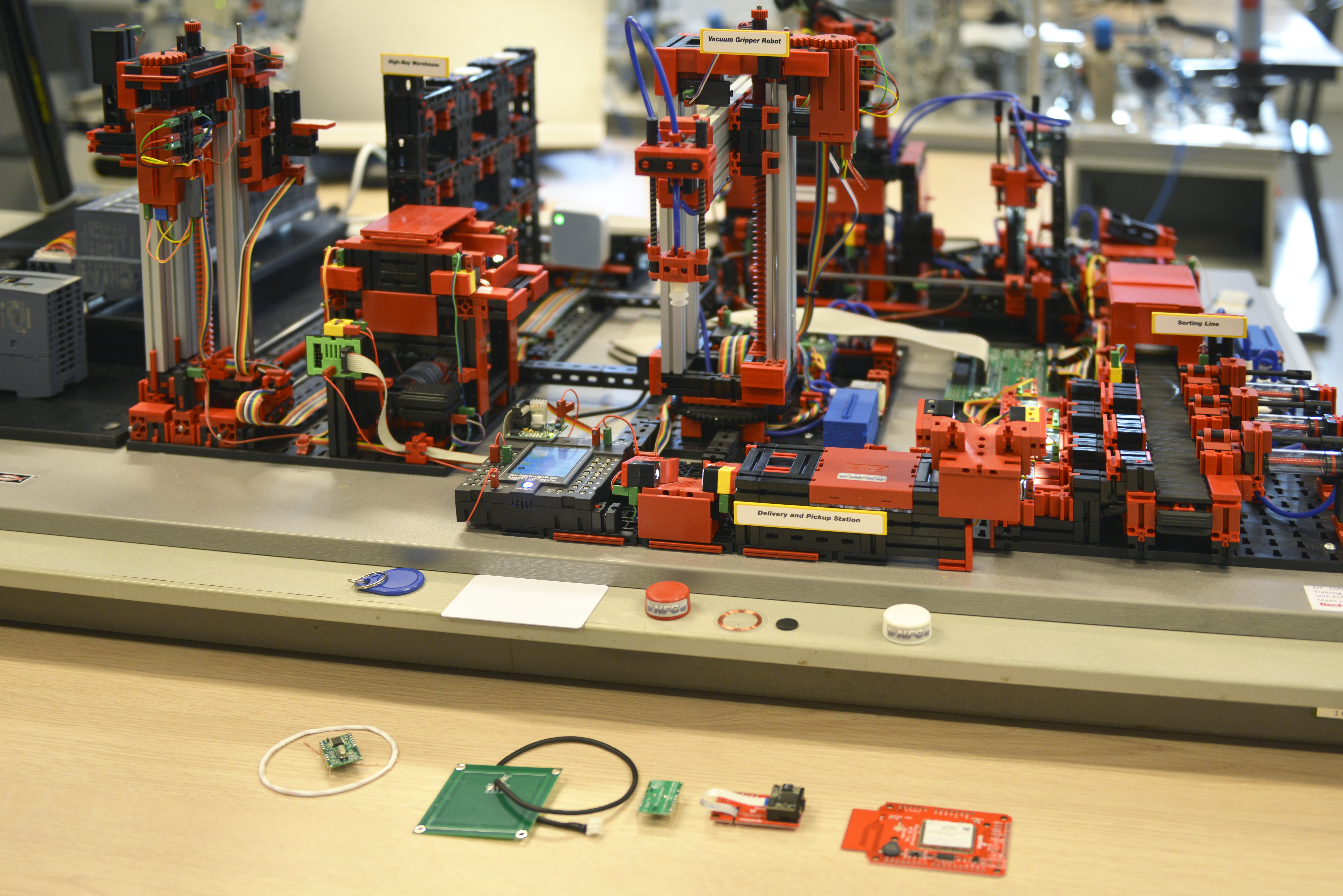
This project is part of the NXTGEN Smart Industry programme, which aims to be a leader in Europe with the best and most flexible manufacturing ecosystem/network. We aim to achieve this by being Industry 4.0 compliant, making us more attractive and competitive for companies looking to outsource their production within the Dutch Next Generation HIGHTECH ecosystem.
Network technologies
The philosophy of the Smart Industry projects and its partners is to implement Industry 4.0-compatible, autonomous and smart network technologies. These are initially applied in pilots and use cases, both for and with the domains in the test and experiment facilities (TEF). At the same time, it actively contributes to the broad integration of these technologies in the manufacturing industry, with demonstrations in the TEF and training modules in collaboration with the Smart Makers Academy.
Industry 4.0 compliant
By Industry 4.0 compliant, we mean, among other things, subject to the application of standards such as Asset Administration Shell (AAS). This involves the production of self-describing parts for digital twins in the factory. We also use IDS/Gaia-X for secure and reliable data exchange across value chains. Applying these standards should lead to a kind of digital plug (and a type of operating system) to which various applications can be connected.
The biggest challenge lies in training current employees to make the most of these digital tools and embrace the new Industry 4.0 standards. To promote national coverage and acceptance, a large number of universities of applied sciences are working within the programme to develop training courses for the NXT GEN community (as part of the consolidation of NXTGEN results) and for lecturers and students of universities of applied sciences. These training courses will also be made available to SME manufacturers and other training institutions through the Smart Maker Academy (SMA).
The role of the research group
Within this project, the Research Group Smart Sustainable Manufacturing is responsible, among other things, for developing teaching materials for the metro line of manufacturing apps and the I4.0 digital connector, including:
- What does the architecture of the future factory look like and what is needed where?
- How do I link the different layers in my factory? Which standards apply where and how do I link the different information sets?
- How do I ensure the safety of different components in my factory?
- How do I develop apps in a uniform way with linked information? What basic apps does each factory have and what methods/techniques are already available for this purpose? (Think Lean / QrM / SPC / ...)
Team
- Jenny Coenen, Lector Smart Sustainable Manufacturing, [email protected]
- Henk van der Burgh, researcher Smart Sustainable Manufacturing, [email protected]