A local future for plastic waste
Jenna and colleagues built a machine to easily reuse plastic.
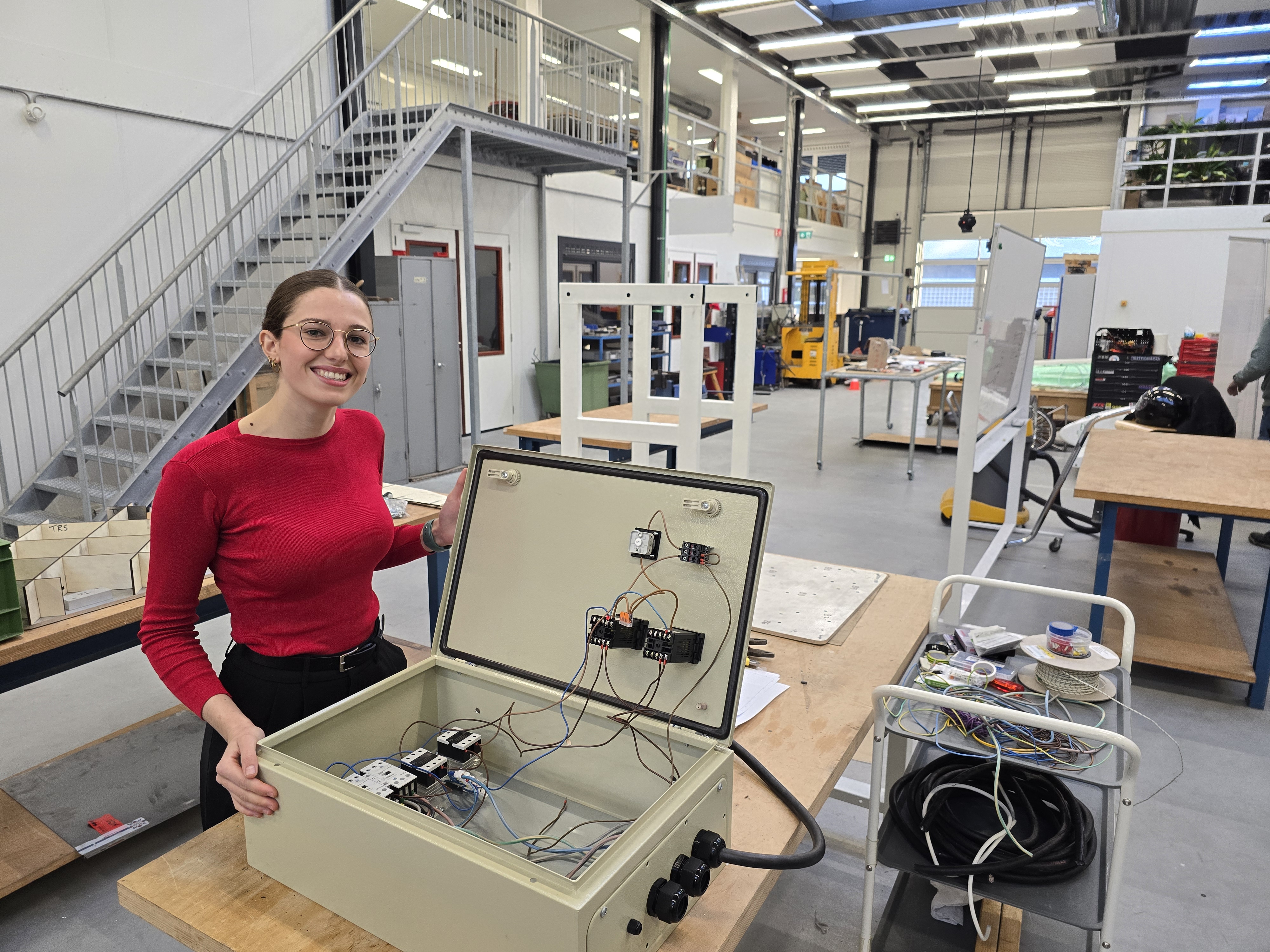
How can you use locally collected plastic to make new products, which you can then sell again in the neighbourhood? At the Beta Factory at our location in Delft, work is underway on a machine that will make just that possible. People with a distance to the labour market will soon be able to use the machine to press sheets from milk cartons and other plastic waste, which can be used on site for all kinds of products; from bicycle crates to chair seats. "They do have to be useful products," says Jenna Coward, driving force behind the realisation of the device. "No unnecessary key rings or earrings that you throw away after a few uses. We want things to last as long as possible and be put to the best possible use."
A few years ago, South African Jenna was looking for a project-based and affordable engineering course in a country that is serious about sustainability and circularity. Themes after her heart. It became the Netherlands and it became De Haagse. "South Africa is a country full of enormous challenges, wicked problems. Education is largely geared to that. You learn in South Africa, is my experience, to think very solution-oriented. The set-up of the industrial design study, partly in The Hague and partly here in Delft at the Sustainable Manufacturing Research Group, fitted in well with that for me.
Special project
After successfully completing her studies with a project around the production of 'funky' bicycle crates made from recycled plastic, Satish Kumar Beella, her graduation supervisor, asked if she wouldn't like to come to The Hague to work on a special project. "An important basis for recycled plastic products are plastic sheets from which you can then cut all kinds of shapes. However, these sheets are very large and, as a small local user, you also always have to buy several sheets at the same time from the factory. This is why the idea arose here at the college: couldn't we build a machine that makes smaller sheets, fed by plastic waste we collect locally?"
The machine is being built for Stichting Stunt, a social enterprise in Delft that makes products from residual materials for (business) clients. Volunteers and people following a learning-working path at Stunt do not see waste as rubbish, but as a raw material from which new products can be made. Like Jenna's bicycle crates. "In our workshop, we all worked together on this machine. Colleagues helping with welding or thinking along about practical solutions. I'm not a mechanical engineer, so I learn a huge amount from this myself. Our workshop coordinator Wouter Nederlof was also invaluable in the project. From welding and cutting out parts to tips on how I should paint the device, we could always turn to him." Oskar Imiolek, who was completing his master's at the Delft campus at the same time as Jenna, supported the project with his knowledge of electrical components.
Meanwhile, work is also underway on a second machine, for the Kringloopwinkel Den Haag. Step after that, the manual on how to build the machine will also be open-sourced to any recycling shop, work-experience site or other organisation that wants to work with local recycled plastic. "We have gratefully used the Precious Plastic network, in which people worldwide think and work together on what a recycling machine should look like. Now we can contribute to open source platforms ourselves."
Sustainably connecting students
This does not conclude the project. "I would like to ensure that our students remain sustainably connected to this recycling process. For example, as designers of new products for which small-scale production is convenient. Also, thanks to the machine, students can make plastic prototypes more easily. Instead of a theoretical exercise, you can now really practically assemble and test a product made of plastic. Students from the sustainable sports minor came here recently and they can now build a prototype skateboard from recycled plastic or other sports products that can be made from recycled plastic. That gives a much better idea of what challenges a product has. We also involve business students in marketing products and identifying new markets."
Jenna continues: "With the machine, we can also set up teaching programmes for primary schools, which in turn we can involve PABO students. Children can now see how recycling plastic waste is done and what you can do with it, an important lesson for the next generation. Of course, you can also organise these workshops for other generations. Recycling then really comes alive." Jenna is working with The Hague's Green Office to reach out and interest students in working with the machine and developing new products.
The Assisted Repair Corner
And Jenna's infectious enthusiasm for sustainability does not stop with the delivery of the machines. The next project is already presenting itself: the Assisted Repair Corner. "A place in the building where colleagues and students are helped to repair things. We want to combat fixophobia with this intersection of a workshop and a service desk, repair is possible in many cases, at least we want to make repair more accessible as an option for everyone." The Repair Corner is also a place where researchers from The Hague can conduct research into what stops and motivates people from fixing things. "The mentality here at school really motivates me," says Jenna. "Working on practically realisable sustainability initiatives, that's what I came here for and that's exactly what I'm doing. Step by step, we are making the world a little more sustainable."
This project was made possible by the Sustainable Manufacturing Research Group, led by colleague Jenny Coenen. The research group offers students and recent graduates the opportunity to develop their research skills and gain practical experience in the field of circular manufacturing.